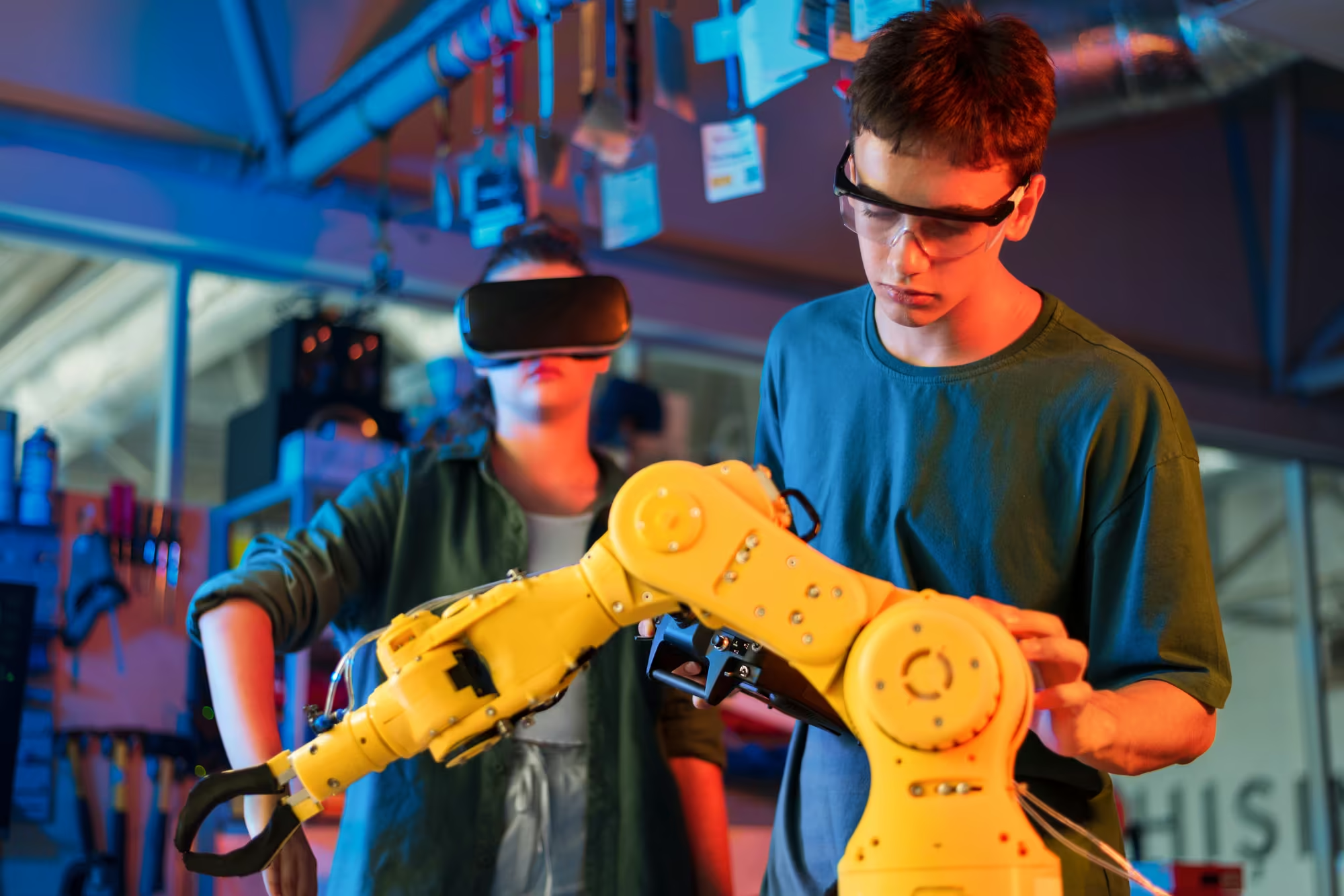
Challenge:
A prominent manufacturing company faced several operational inefficiencies that were hindering their ability to meet increasing market demands. These challenges included outdated systems, fragmented workflows, and a lack of real-time visibility into production performance. The reliance on manual processes was driving up costs, slowing down production cycles, and increasing the risk of errors. Faced with rising competition and the need for enhanced operational agility, the client sought a transformative solution to streamline their operations and scale their business effectively.
Solution:
TTG stepped in as a strategic partner to design and implement a tailored solution that addressed the company’s unique challenges. First, our experts conducted an in-depth assessment of the client’s existing processes and technological infrastructure. Based on these insights, we developed and deployed an integrated manufacturing execution system (MES) that provided real-time performance monitoring and enhanced workflow automation. Additionally, the MES was seamlessly integrated with supply chain and enterprise resource planning (ERP) systems to ensure a unified and efficient ecosystem.
To support change management and adoption, we conducted comprehensive training sessions for the team and maintained close collaboration throughout the implementation process. Leveraging data analytics features within the system, the company gained actionable insights that enabled proactive decision-making and continuous process optimization.
Impact:
The implementation of TTG's solution delivered significant results for the client. Operational efficiency improved by 45%, with production cycles becoming faster and more reliable. Real-time visibility into manufacturing processes enabled the company to identify bottlenecks quickly and implement resolutions without delays. The automation of previously manual tasks reduced errors by 35%, which led to notable cost savings. Additionally, the integration of the MES with existing systems resulted in more cohesive operations and smoother communication between departments.
Perhaps most importantly, the client was able to scale its production capacity to meet growing market demand without compromising on quality. This operational transformation not only positioned the company as a competitive industry leader but also solidified its reputation for innovation and reliability in the manufacturing sector.
Results
- 45% Improvement in Operational Efficiency
Streamlined workflows and automated processes eliminated redundancies and reduced delays, setting a new benchmark for productivity.
- 35% Reduction in Errors
Automated manual tasks enhanced system accuracy, significantly cutting costs while elevating product quality.
- 30% Faster Production Cycles
Accelerated timelines empowered the company to reliably meet growing market demand with unmatched consistency.
- Real-time Visibility into Production Processes
Leadership gained a proactive edge by identifying and resolving bottlenecks before they caused downtime, further driving productivity gains.
Beyond Day-to-Day Gains:
By seamlessly integrating the MES with ERP and supply chain systems, the client created a unified, agile ecosystem that improved communication and decision-making across departments. This cohesion not only optimized production but also unlocked scalable capacity, enabling the company to expand confidently without compromising quality.
A Strategic Leap Forward:
This transformation transcended operational improvements. It entrenched the client’s position as an industry leader, ready to adapt and thrive in an evolving market. Through TTG’s advanced technology and expertise, inefficiencies were minimized, processes were optimized, and a strong foundation for growth and innovation was forged.
TTG didn’t just enhance operations—it reimagined what success could look like.